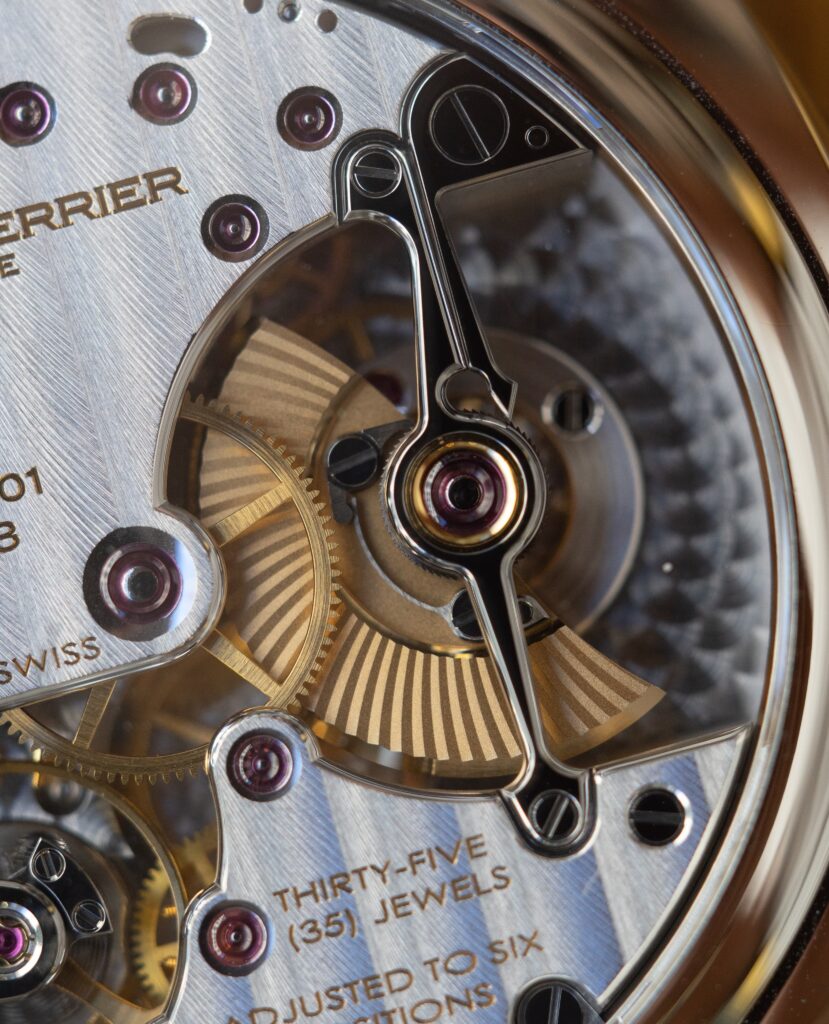
Introduction
In the realm of haute horlogerie, few techniques exemplify the pinnacle of craftsmanship quite like anglage. This meticulous art of beveling and polishing the edges of watch components is a hallmark of fine watchmaking, elevating timepieces from mere instruments to works of art. Anglage, derived from the French word “angle,” refers to the creation of a polished, angled surface along the edges of watch parts, typically at a 45-degree angle.
The practice of anglage dates back to the 18th century, evolving alongside the watchmaking industry itself. Initially developed as a method to remove sharp edges that could potentially damage other components or catch debris, anglage has since transformed into a revered decorative technique. Today, it stands as a testament to a watchmaker’s skill and a brand’s commitment to excellence.
The Technique of Anglage
At its core, anglage is a process of carefully filing and polishing the edges of watch components to create a smooth, reflective surface. This technique is applied to various parts within a watch movement, including bridges, plates, levers, and even some smaller components like spring cocks.
The process begins with the careful marking of the edge to be beveled. Traditionally, this is done by hand using a fine-tipped marker or scribe. The artisan then uses a series of files, starting with coarser grits and progressing to finer ones, to shape the edge at a precise 45-degree angle. This angle is crucial, as it allows light to reflect off the surface in a way that accentuates the finish and adds depth to the movement’s appearance.
After filing, the real artistry begins with the polishing phase. Watchmakers use a variety of tools for this step, including wooden pegs, abrasive pastes, and specialized polishing stones. The most traditional method involves a gentian wood stick, chosen for its unique fiber structure that allows for a high polish without scratching the metal surface. The artisan applies polishing compound to the wood and carefully works the beveled edge, gradually achieving a mirror-like finish.
There are several types of anglage, each with its own characteristics:
- Rounded Anglage: This classic style features a smoothly curved bevel that transitions seamlessly from the top surface to the side of the component.
- Flat Anglage: As the name suggests, this type maintains a flat surface on the bevel, creating a sharp, crisp edge.
- Inward Anglage: One of the most challenging techniques, inward anglage involves creating a bevel on interior angles or cutouts within a component.
- Outward Anglage: This is the more common form, applied to the outer edges of components.
The choice of anglage style often depends on the watch’s overall design, the specific component, and the desired aesthetic effect.
The Artistry Behind Anglage
Mastering the art of anglage requires years of practice and an exceptional eye for detail. The process is as much about feel and intuition as it is about technical skill. Master craftsmen develop an almost symbiotic relationship with their tools, able to sense the slightest variations in pressure and angle that can make the difference between a flawless finish and a ruined component.
One of the most challenging aspects of anglage is maintaining consistency. The bevel must be uniform in width and angle along the entire length of the edge, even when that edge curves or changes direction. This requires not only steady hands but also a deep understanding of how different metals behave under the file and polish.
While machines can now perform basic anglage, true connoisseurs prize hand-finished components. The subtle imperfections and unique character imparted by hand-finishing are considered marks of superior craftsmanship. These minute variations, invisible to the naked eye but discernible under magnification, add a warmth and personality to the watch that machine-finished parts cannot replicate.
The aesthetic considerations in anglage go beyond mere shininess. The interplay of light and shadow created by perfectly angled bevels can dramatically enhance the visual depth and complexity of a watch movement. Skilled artisans consider how each beveled edge will interact with others in the movement, creating a harmonious overall effect that draws the eye and rewards close inspection.
Technical Challenges in Anglage
The execution of fine anglage presents numerous technical challenges, each requiring specific skills and techniques to overcome:
Material Considerations: Different metals used in watchmaking respond differently to the anglage process. Brass, commonly used for plates and bridges, is relatively soft and easy to work with but can be prone to scratching. Steel, used for many functional components, is harder and more resistant to polishing. Gold, sometimes used in high-end movements, is soft but can be “gummy,” making it challenging to achieve clean edges. Each material requires a slightly different approach and set of tools.
Precision and Tolerances: The margin for error in anglage is incredibly small. Bevels are typically between 0.15mm and 0.4mm in width, and maintaining this consistency along complex shapes requires exceptional control. Over-polishing can round edges too much, potentially affecting the component’s fit or function within the movement.
Working with Intricate Shapes: Many watch components feature complex geometries, including tight curves, sharp corners, and narrow arms. Applying consistent anglage to these shapes is particularly challenging, often requiring specially shaped tools or innovative techniques.
Inward Angles: Perhaps the most difficult aspect of anglage is the treatment of inward angles. These acute interior corners cannot be reached with standard files or polishing tools. Instead, they must be painstakingly finished by hand using tiny handmade tools or, in some cases, abrasive thread.
Surface Preservation: While working on the edges, it’s crucial to avoid damaging the flat surfaces of the component. This requires careful control and often the use of protective coatings or tapes on areas not being worked on.
Time Management: Fine anglage is extremely time-consuming. A single bridge might require several hours of work to achieve a perfect finish. Balancing the desire for perfection with the practical constraints of production is an ongoing challenge for watchmakers.
Anglage in Modern Watchmaking
In contemporary haute horlogerie, anglage continues to play a crucial role, both as a mark of quality and as a canvas for innovation. Many high-end watch brands have developed their own signature styles of anglage, pushing the boundaries of what’s possible with this traditional technique.
For example, some manufacturers have experimented with varying the width of bevels to create dynamic visual effects. Others have incorporated contrasting finishes within the same component, such as combining polished bevels with frosted flat surfaces for enhanced contrast.
The rise of skeletonized and open-worked watch designs has placed even greater emphasis on movement finishing, with anglage taking center stage. In these watches, where the movement is fully visible, the quality of anglage can make or break the overall aesthetic.
Notable examples of exceptional anglage can be found in watches from brands like A. Lange & Söhne, known for their wide, immaculately polished bevels, or Philippe Dufour, whose movements are considered the gold standard in hand-finishing. Independent watchmakers like Kari Voutilainen, Roger W. Smith and Romain Gauthier have also gained recognition for their extraordinary attention to anglage and other finishing techniques.
While the art of anglage is deeply rooted in traditional hand-craftsmanship, it’s important to understand that even high-end watches often begin their journey with CNC (Computer Numerical Control) machining. This modern approach to initial component production offers several advantages:
- Precision: CNC machines can achieve extremely tight tolerances, often beyond what’s possible by hand.
- Consistency: Each component produced by CNC is virtually identical, ensuring uniformity across production runs.
- Efficiency: CNC allows for faster production of base components, reducing overall manufacturing time.
However, CNC is merely the starting point in fine watchmaking, not the final step. The machine-produced parts serve as a canvas for the true artistry of hand finishing.
Limitations of CNC in Anglage
Despite its advantages, CNC has significant limitations when it comes to achieving the highest standards of anglage, particularly with interior angles. Most manufacturers face an insurmountable challenge when attempting to create sharp interior angles using CNC alone:
- Geometric Constraints: CNC tools are typically cylindrical, making it impossible to cut a perfectly sharp interior corner. The smallest possible radius is limited by the diameter of the cutting tool.
- Tooling Limitations: Even the finest CNC cutting tools cannot match the precision and flexibility of hand tools wielded by skilled artisans.
- Material Considerations: The high-speed rotation of CNC tools can cause unwanted effects on the metal surface, particularly in softer materials like brass or gold.
These limitations mean that true haute horlogerie finishing, especially for interior angles, necessitates hand finishing. Only through meticulous hand work can watchmakers achieve the sharp, polished interior angles that connoisseurs prize.
The Interplay of CNC and Hand Finishing
In modern high-end watchmaking, there’s a delicate balance between leveraging CNC technology and preserving traditional hand-finishing techniques:
- Initial Production: CNC is used to create base components with high precision and consistency.
- Rough Anglage: Some manufacturers use CNC to create a basic anglage profile, which serves as a starting point for hand finishing.
- Hand Finishing: Master craftsmen then take over, refining the angles, creating sharp interior corners, and applying the final polish that gives anglage its characteristic gleam.
This combination allows watchmakers to maintain production efficiency while still delivering the exquisite finishing that defines luxury timepieces.
Identifying True Hand-Finished Anglage:
For collectors and enthusiasts, understanding the interplay between CNC and hand finishing is crucial in appreciating and evaluating fine watches:
- Interior Angles: Sharp, perfectly polished interior angles are a clear sign of hand finishing, as these cannot be achieved by CNC alone.
- Consistency vs. Character: While CNC produces perfectly uniform results, hand-finished components may show subtle variations that attest to their artisanal nature.
- Surface Quality: The depth and quality of the polish on angled surfaces often reveal whether they’ve received extensive hand attention.
By recognizing these details, collectors can better appreciate the value proposition of watches that combine the precision of CNC with the artistry of hand-finished details.
The Future of Anglage
As we look to the future, the art of anglage faces both challenges and opportunities. On one hand, the increasing sophistication of manufacturing technology threatens to make traditional hand-finishing obsolete. CNC machines and even 3D printing technologies are becoming capable of producing ever-finer finishes, potentially reducing the need for skilled hand-finishing.
However, the very exclusivity and human touch that hand-finished anglage represents may ensure its continued relevance. In a world of mass production, the value placed on handcrafted luxury items is likely to increase. We may see a bifurcation in the market, with machine-finished anglage becoming more prevalent in mid-range watches, while high-end pieces double down on traditional hand-finishing as a key differentiator.
Innovation in materials may also shape the future of anglage. As watchmakers experiment with new alloys, ceramics, and even sapphire components, new techniques and tools will need to be developed to apply traditional finishing methods to these modern materials.
There’s also potential for anglage to evolve beyond its traditional form. Some avant-garde watchmakers are already experimenting with asymmetrical bevels, intentionally “imperfect” finishes, or combining anglage with other decorative techniques to create entirely new aesthetic effects.
Appreciating Anglage as a Collector
For watch enthusiasts and collectors, understanding and appreciating fine anglage can add a new dimension to the enjoyment of haute horlogerie. Here are some tips for evaluating anglage:
- Consistency: Look for uniform width and angle of the bevels, even around curves and corners.
- Sharpness: Edges where the bevel meets the flat surface should be crisp and well-defined.
- Polish: The beveled surfaces should have a mirror-like finish, free from scratches or clouding.
- Inward Angles: Pay special attention to interior corners. Clean, sharp inward angles are a sign of exceptional craftsmanship.
- Interaction with Light: Well-executed anglage will create beautiful plays of light as you move the watch, with bevels catching and reflecting light distinctly from the flat surfaces.
- Overall Harmony: Consider how the anglage integrates with other finishing techniques and the overall design of the movement.
When examining a watch, don’t hesitate to use a loupe or microscope. Many of the finest details in anglage are best appreciated under magnification. Remember that even in high-end watches, it’s unrealistic to expect every single component to have perfect hand-finished anglage. Focus on the most visible parts and those that would have the greatest impact on the overall aesthetics.
Conclusion
The art of anglage represents the intersection of functionality, craftsmanship, and artistic expression in watchmaking. It transforms the utilitarian edges of mechanical components into miniature sculptures, elevating the entire watch from a mere timekeeping device to a work of art.
As we’ve explored, achieving mastery in anglage requires not only technical skill but also patience, artistic vision, and a deep respect for horological tradition. It’s a testament to human skill and perseverance in an age of increasing automation.
Whether you’re a seasoned collector or new to the world of fine watches, understanding and appreciating anglage can enrich your horological journey. It offers a window into the painstaking work that goes into creating truly exceptional timepieces and serves as a reminder of the enduring value of human craftsmanship in our modern world.
As watchmaking continues to evolve, the art of anglage will undoubtedly evolve with it. Yet, its fundamental purpose – to add beauty, refinement, and a human touch to mechanical artistry – will likely remain unchanged, ensuring its place as a cornerstone of haute horlogerie for generations to come.